Strengths & Weaknesses for Quality Engineer Freshers
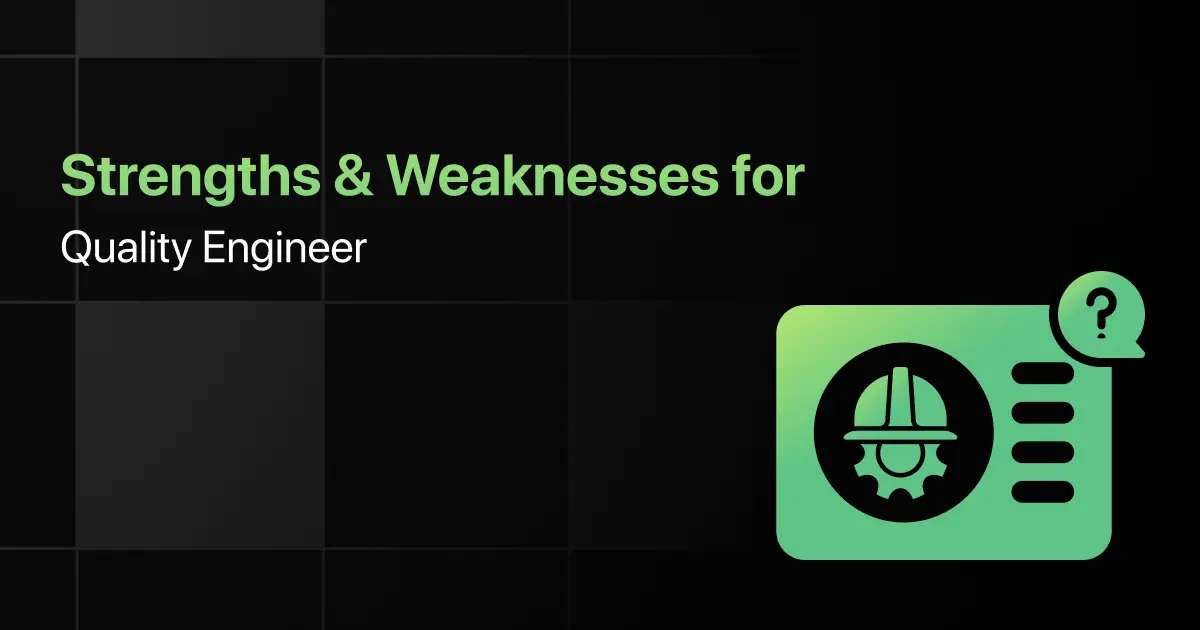
For quality engineers, job interviews are not just about technical knowledge but also about attention to detail and problem-solving skills.
One of the biggest challenges is explaining their strengths and weaknesses in a way that makes a good impression.
This blog will help with strengths & weaknesses for quality engineers.
Strengths for Quality Engineer Interviews
Below are the 3 strengths for quality engineers for interviews:
1. Expertise in Root Cause Analysis
Root cause analysis (RCA) is essential for quality engineers to identify and eliminate defects in manufacturing or process workflows.
Instead of just fixing symptoms, RCA helps find the actual cause of a problem, leading to long-term improvements.
Techniques like the 5 Whys, Fishbone Diagram, and Failure Mode and Effects Analysis (FMEA) ensure products meet quality standards consistently.
Template Version:
“At [Your Previous Company], I used root cause analysis to solve [specific issue, e.g., ‘high defect rates in our production line’].
By applying [specific technique, e.g., ‘the 5 Whys and FMEA’], I identified that [specific root cause, e.g., ‘a supplier material inconsistency’] was the main issue.
Fixing this led to a [specific result, e.g., ‘30% reduction in defects and improved production efficiency’].”
Logic Behind This:
This version highlights a real-world problem, the RCA technique used, and a measurable impact, making the skill more tangible for interviewers.
Mistakes to Avoid:
Don’t just say, “I’m good at problem-solving”—explain how you analyze and fix problems.
Avoid vague statements; always provide a specific problem and solution.
Don’t forget to mention the impact of your solution (e.g., defect reduction, cost savings).
2. Strong Knowledge of Quality Standards
Quality engineers must ensure that products and processes comply with industry standards like ISO 9001, Six Sigma, and Lean Manufacturing.
Understanding these frameworks helps improve efficiency, reduce waste, and maintain consistent quality across production.
Companies rely on quality engineers to implement and monitor these standards to meet regulatory requirements.
Template Version:
“At [Your Previous Company], I led the implementation of [specific standard, e.g., ‘ISO 9001:2015’], ensuring our processes met strict quality guidelines.
By introducing [specific improvement, e.g., ‘a Lean Six Sigma approach to minimize process variations’], we reduced [specific issue, e.g., ‘production waste by 25%’].”
Logic Behind This:
This version makes it clear how applying quality standards leads to tangible improvements in production, efficiency, or compliance.
Mistakes to Avoid:
Don’t just list standards—explain how you applied them in real projects.
Avoid generic statements like “I know Six Sigma” without mentioning how you used it.
Don’t forget to highlight measurable improvements in quality or efficiency.
3. Proficiency in Statistical Process Control (SPC) & Data Analysis
SPC and data analysis are critical for monitoring production processes and detecting variations before they cause defects.
By using statistical tools like control charts, histograms, and process capability analysis, quality engineers can make data-driven decisions to maintain consistency and reduce variability in manufacturing.
Template Version:
“At [Your Previous Company], I implemented Statistical Process Control (SPC) to monitor [specific process, e.g., ‘assembly line defect rates’].
By using [specific tool, e.g., ‘control charts and process capability analysis’], I detected early variations and adjusted processes, reducing defect rates by [specific result, e.g., ‘20%’].”
Logic Behind This:
This version clearly shows the application of SPC tools, the problem they solved, and the measurable improvement they brought.
Mistakes to Avoid:
Don’t just mention SPC—explain how you used it to improve quality.
Avoid general statements like “I use data for quality control” without examples.
Don’t forget to highlight the direct impact on defect reduction or process stability.
Weaknesses for Quality Engineer Interviews
Below are the 3 weaknesses for quality engineers for interviews:
1. Limited Hands-On Experience with Automation Tools
Automation tools like Selenium, JIRA, or TestComplete are important for improving efficiency in quality testing.
If a quality engineer has limited experience with these tools, manual testing can take longer, and automation opportunities may be missed.
Template Version:
“In my previous roles, I mostly focused on manual testing and had limited hands-on experience with automation tools like [specific tool, e.g., ‘Selenium’ or ‘JIRA’].
To improve, I have started taking online courses and working on small test automation projects to develop my skills.”
Logic Behind This:
This answer acknowledges the gap while showing a proactive approach to learning.
It reassures the interviewer that you understand the importance of automation.
Mistakes to Avoid:
Don’t say automation isn’t necessary—companies value efficiency.
Avoid making it sound like you resist learning new tools.
Don’t just admit the weakness—always mention how you’re improving.
2. Struggles with Cross-Department Communication
Quality engineers need to work with multiple teams like development, production, and customer support.
If communication isn’t clear, misunderstandings can lead to defects, delays, or inefficiencies.
Template Version:
“I’ve realized that explaining quality concerns to non-technical teams can sometimes be challenging.
To improve, I have been practicing clearer communication, using simple language, and providing more visual reports to make quality issues easier to understand.”
Logic Behind This:
This is a good answer because it acknowledges the challenge and offers a clear strategy to improve.
It shows that you are making an effort to bridge communication gaps.
Mistakes to Avoid:
Don’t blame others for communication issues—take responsibility.
Avoid using too much technical jargon when explaining problems.
Don’t ignore the importance of teamwork—show that you value collaboration.
3. Overemphasis on Compliance, Slowing Innovation
Following industry regulations and standards is crucial, but being too focused on compliance can sometimes slow down new ideas or process improvements.
A balance between compliance and innovation is necessary.
Template Version:
“I always prioritize compliance to ensure quality and safety, but I’ve realized that sometimes this can slow down innovation.
To improve, I am learning to assess risks better and find ways to maintain compliance while also supporting efficiency and new ideas.”
Logic Behind This:
This answer works well because it highlights your commitment to quality while showing that you are working on being more flexible.
Mistakes to Avoid:
Don’t say compliance isn’t important—companies must follow regulations.
Avoid making it sound like you resist change or new methods.
Don’t ignore efficiency—show that you are working on balancing both
Final Words
In the end, being able to talk about your strengths and weaknesses in a quality engineering interview can help you make a strong impression.
By being honest about your skills and showing a willingness to improve, you prove that you’re committed to ensuring high-quality standards in your work.
Frequently Asked Questions
1. What key strengths should a quality engineer mention during an interview?
Quality engineers should highlight attention to detail, strong knowledge of quality standards, experience with testing and inspection processes, and proficiency in tools like Six Sigma or Lean methodologies.
2. What are the most common weaknesses of quality engineers?
Common weaknesses include difficulty in managing tight deadlines, limited experience with certain quality control tools, and challenges in communication with other departments.
3. How can quality engineering freshers identify their strengths and weaknesses?
Freshers can identify their strengths and weaknesses by reviewing academic projects, internships, seeking feedback from mentors, and evaluating their performance in team settings or simulations.
4. How can quality engineers frame their weaknesses in a positive way during interviews?
Quality engineers can frame their weaknesses in a positive way by focusing on those they are actively improving and demonstrating their willingness to learn, adapt, and grow.
5. What technical skills should quality engineers emphasize in job interviews?
Quality engineers should emphasize knowledge of quality control techniques, testing methodologies, statistical analysis, familiarity with quality management systems (QMS), proficiency in tools like Excel, Minitab, and experience with audits or certification processes.
Related Posts
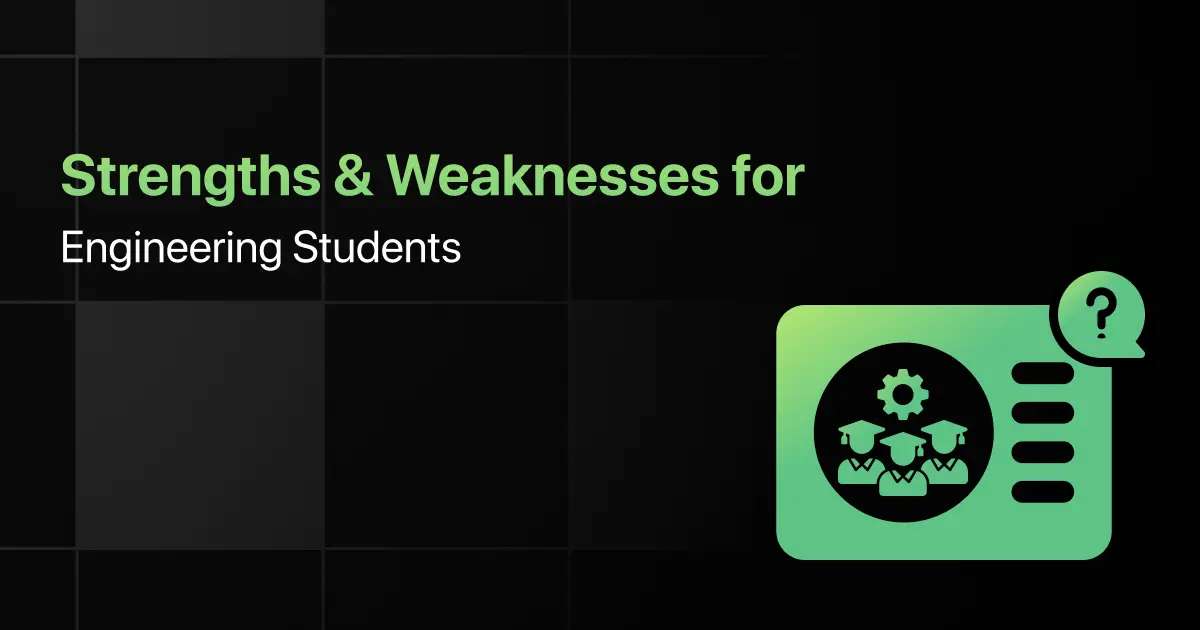
Strengths & Weaknesses for Engineering Students Freshers
For engineering students, job interviews can feel challenging because they are just starting their careers. One of the toughest parts is …